THANK YOU FOR SUBSCRIBING
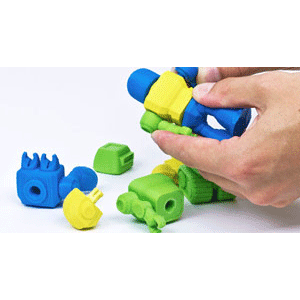
John Alpine, VP of Global Software, 3D Systems
30 years ago, 3D Systems’ Chuck Hall created one of the most transformative inventions to change manufacturing since Henry Ford invented the assembly line. It is called 3D Printing.
Today 3D printing is changing nearly every aspect of modern product manufacture, whether its prototypes, bespoke medical implants or tire molds, there is almost no area of product manufacturing that it hasn’t touched.
"To reduce risks and increase flexibility of incorporating market feedback, small batch product runs where a few hundred units of a product are produced are shipped to customers who then provide feedback."
However, for many companies the technology is still very new, and while fascinated, they want to "try before buy" or often the volume they require is too small to justify a purchase of 3D Printers. The solution to this has been provided by the growth of 3D Service bureaus like 3D Systems’ Quickparts.
A 3D printing service bureau requires no capital investment or special training around printing equipment on the part of customers. Most services offer instant quoting so that the costs are known before a dollar is spent. 3D files are simply sent over the internet, and, using advanced cloud-based cost estimation software, quotes are immediately delivered with no obligation to buy.
The advantage of a service bureau is not only lower upfront costs, but the variety of materials and printing processes that they support. Similar to traditional subtractive manufacturing, 3D printing offers a large variety of processes and materials to meet almost every manufacturing need. A printing service can guide your engineering team into choosing the optimal printing process and material for the particular part.
One of the most amazing things with 3D Printing is that the cost of a part is related only to material and part size, but not part complexity. This is completely unique in the manufacturing world today where the more complex the shape of the part, the higher its manufacturing cost. To a 3D printer, which lays down material one very thin layer at a time, part complexity has no effect on the build process. 3D Printing can even manufacture fully assembled parts.
How does it work?
Designers create a design in 3D CAD software using the same tools and processes used for traditional part design and manufacture. Nearly every major CAD package today supports the export of formats compatible with 3D printing. With many
Once an engineer has created a 3D model of a part for manufacture, it’s typically analyzed for “printability”. Advanced printing bureaus offer free software that can analyze CAD files for their suitability for printing and any issue they might have on a process and material basis. Some designs may be printable in one technology but not another. Different material can affect strength or basic minimum geometric dimensions (for example parts with thin walls and feature sizes). To help deal with this, 3DSystems offers free web and desktop-based analysis and file repair software called 3DSPRINT that replaces older expensive and complex software that did this task. This software can analyze files for issues but also provide repair and editing tools that can reduce the cost of parts by shelling (hollowing) selective pattern filling.
Cloud based manufacturing
3D printing, while offering unique capability not found in traditional manufacturing is not always the best choice for all products. Some products will still be manufactured with milling, mold or other traditional subtractive manufacturing processes. The startup cost for this type of traditional manufacturing in house can be extremely high. One of the more recent trends is that the 3D printing revolution also spawned a revolution in rapid manufacturing services across the whole spectrum of the industry: Using the same 3D design process and service bureaux, engineering can request a part to be 3D printed, milled from stock, built from sheet metal or stamp/molded all from the same provider. Engineers can even move between manufacturing processes, first printing a prototype part, and then with the same service, submit the part for a traditional manufacturing process. This capability supports the trend in product companies where products are introduced to the market in small batches. To reduce risks and increase flexibility of incorporating market feedback, small batch product runs where a few hundred units of a product are produced are shipped to customers who then provide feedback. The feedback is then iterated into the design, and because no expensive tooling up was used, a new design can be iterated at far lower costs.
What’s next?
Another trend in design is to take advantage of both printing service bureaus as well as in-house printing capability. As printer costs have decreased companies find that having in-house printing capacity decreases design times by delivering fully functional prototypes in just hours. New generation of low cost printers such as the Cube 3 or Cube Pro is able to produce colored plastic parts in PLA or ABS that are dimensional accurate and fully functional. New generations of printable materials such as nylon are expanding the capability of these low-cost printers to handle fully functional stress-resistant parts. As the industry has matured, even the cost of production machines has come down to the point where even modest-sized product companies can consider an in-house printer purchase. Choosing a company that provides both 3D printers and print services means that the same design workflows and cloud-based analysis software is used for either in-house printing or printing with the service bureau.
How to get started?
If your engineering team is already designing in 3D then getting started is as simple as clicking on a 3D print service URL such as quickparts.com and uploading the design. Most bureaus’ web sites contain simple guidelines for the engineer such as part size limits, descriptions of material types and FAQs. Typically companies try out pricing and small patch production of parts. Once costs are calculated and workflow successfully established, the capability can be rolled out to the whole engineering organization.
Given the relatively low cost of small batch prototype parts, that the process fits into current workflow and the software needed can be both simple and free, it’s no wonder that this aspect of the market has been the fastest growing segment in manufacturing.